Food & Beverage
We understand the specialist needs of the food and beverage industry, and our food, beverage and confectionery projects are designed and manufactured to the highest standards.
Food, beverage and confectionery projects include:
90°/180° Modular belting type conveyors
Knife edge conveyors
Plastic modular belt type conveyors
Slat band conveyors
Operational Advantages
Systems designed with operator ergonomics in mind
Open design construction for hygienic applications
Large range of belt types to suit specific applications
Integrated controls package
Initiative designs to provide plant flexibility
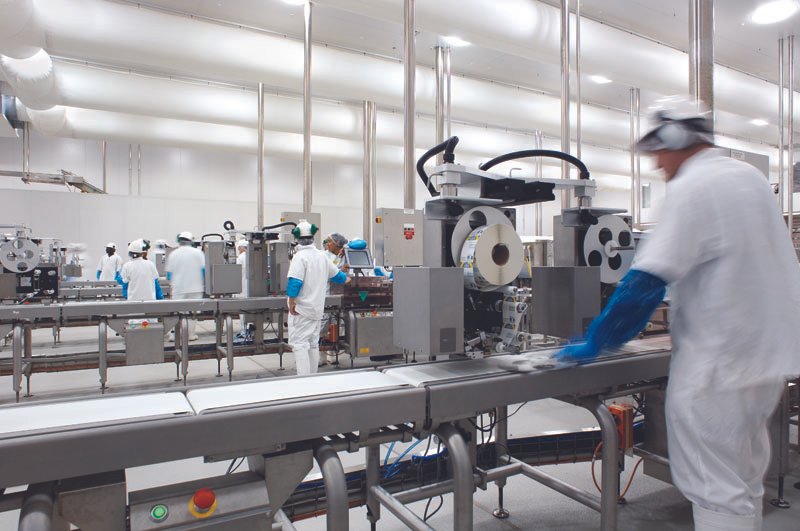
Meat Processing
We specialise in developing componentry and full turnkey systems for abattoirs of all sizes, from family run operations to large scale producers and exporters.
Top 5 reasons abattoir operators are automating processes
-
1. Better resource optimisation
Automation enables abattoir operators to optimise time, money, labour and raw materials. This increases throughput and leads to greater overall profitability.
-
2. Upgrading existing infrastructure equips abattoirs to compete for global and domestic markets
Foreign trade: Export has long been the backbone of the Australian economy. Increasing demand from China for fresh, safe and 100% traceable beef has only added to this. The FTA will lead to reduced tariffs over time and many beef exporters are investing in capital infrastructure now in readiness for increasing international demand for Australian meat. For the first time Chinese consumers can purchase Australian beef online – however, they expect fast, fresh, safe and 100% traceable meat every time. Traditional abattoirs that don’t invest in automation will find themselves being left behind.
Domestic market: While foreign consumers – particularly the Chinese middle classes – are increasingly turning to Australian beef for its freshness and quality, the greatest threat on home soil is competition from cheap overseas imports. Local meat processing plants are investing in automation to optimise resources (time, money, raw materials and labour) to be competitive in the domestic market and offer consumers the best value proposition.
-
3. Keeping pace with consumer demands: paddock to plate identification
The 21st century consumer is prepared to pay a premium for niche products – organic, antibiotic free, brand name, breed specific, Halal and Kosher – every niche market is catered for. On the one hand consumers are willing to pay top dollar, but on the other they want a guarantee that what they’re getting is genuine. Thanks to modern tracking, tracing and automation, paddock to plate identification has never been easier and it’s not just the food regulators who are demanding it.
-
4. Biosecurity, food hygiene and safety
The demand for paddock to plate identification is not just a consumer trend; mandatory process traceability in the meat sector reduces contamination and aids biosecurity measures. Australia is renowned for producing clean, green and safe meat products and this has traditionally underpinned its exporting success. Traceability and quality assurance measures are commonplace across the globe to ensure market access and growth in demand.
Traceability refers to the tracking of any food through all stages of production, processing and distribution (including importation and retail). It means that movements can be traced one step forward and one step backward at any point in the supply chain. The problem with this methodology is that it doesn’t account for the tracing of raw materials through the factory and into the finished product. For this reason, many plants are investing in sophisticated automation and technology systems with the capacity to trace the meat right down to the raw materials.
-
5. Aids organisational/operational intelligence
Automation doesn’t just replace manual labour; it performs tasks that humans cannot. This enables people to be redeployed elsewhere in the business where they can better add to its value. As a result, the overall efficiency of the operation improves as does organisational intelligence.
We have turnkey packages for:
Tote storage, delivery and retrieval systems
Automated tote stackers / elevators
Tote lowerator / tipper units
Cryovac tray handling systems
Trim cutting tables
Final cut packing tables for Cryovac trays
Boning Room Layout
Operational Advantages
Systems designed with operator ergonomics in mind.
Open design construction for hygienic applications.
Large range of belt types to suit specific applications.
Integrated controls package.
Innovative designs to provide plant flexibility
Our past clients include:

Dairy Processing
ICA designed and manufactured equipment meets the highest global standards for safety and hygiene, ensuring Australian dairy is the best in the world.
Capabilities
Milk crate handling systems
Crate and tote washers
Top out de-stackers
Milk crate stackers
Milk crate palletisers
Merge lines
Single filer units
Cheese block processing systems
Powder handling systems
All washers have separate rinse, wash and drying zones to make sure that the crates or totes are completely washed and dried.
Contact us.
Our highly experienced team provide a complete in-house service including engineering, design, manufacture, supply, installation, electronic process control from concept through to commissioning, along with custom training and ongoing site support.
(03) 5440 5100
145 - 147 Howard Street, Epsom, VIC 3551